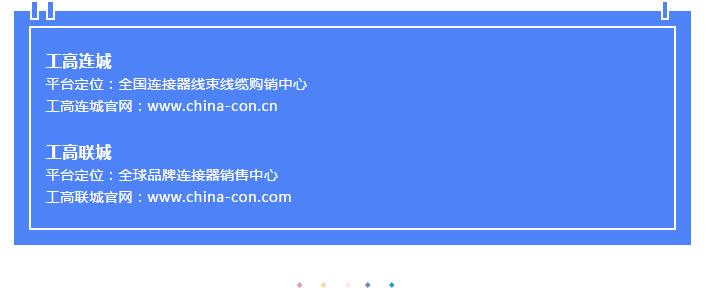
随着运输技术的发展,连接器行业正在向新一代小型化、轻型化、多功能的趋势迈进。
许多汽车连接器已经在市场上销售了几十年。现代汽车、轻型卡车和摩托车等都在使用传统连接器。运输技术已经发生了很大的变化。为了应对消费者对更安全、更智能、更环保的汽车需求,交通技术正在取得重大进步。这些发展往往使设计师和OEM制造商有必要寻找新的互连解决方案。车辆推进系统的新发展是这一任务的关键驱动力。例如以下因素:* 轻度混合动力汽车(也称为动力辅助混合动力车和电池辅助混合动力车)配备额外的48-60V电池系统。* 插电式混合动力和全电动汽车有另外的电动和电子系统。电机、逆变器和充电机构之间需要连接器。此外,汽车中电子产品的普及,尤其是小汽车、轻型卡车等,意味着比以往任何时候都有更多的电气连接。即使是低端汽车现在也有30-50个电子控制单元(ECUs),而一辆豪华车可以有多达150个ECU。与此同时,一辆技术含量高的汽车可以拥有多达65个中央处理单元(cpu),这需要另一种技术上的连接器。当高压互连系统起作用时,电气设计还必须考虑到间隙和爬电情况。由于高压应用的连接器通常比之前的12V接口要大,这可能会造成另一个设计问题。更重要的是,所有的连接都必须容纳在相同的有限空间内,这就造成了空间挑战,因为电动汽车系统中的整体电缆和连接器体积较大。随着OEM厂商将更高水平的功能集成到车辆中,互联单元的数量就会不断增加,电力需求也在不断增加。然而,设计空间在很大程度上仍然是有限和不变。微型化一直是多年来行业的主要趋势,紧凑型连接器是解决方案之一。因此,在研究互连系统时,要寻找紧凑的尺寸和功率处理的最佳组合。
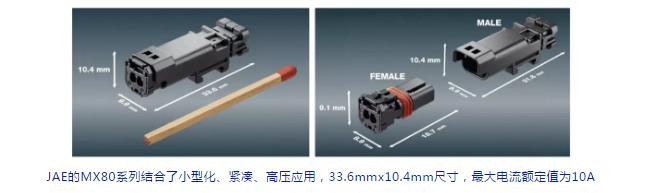
选择更紧凑的连接器通常意味着功能上可能要做出妥协或牺牲。然而,今天,连接器供应商提供了范围扩大的高可靠性小型连接器,满足全球OEM规范的温度,振动,和密封性能。这些互连系统还具有二次锁定、夹子保持器功能、锁存保护和其它选项。连接器系统电线范围宽可为整个车辆应用系统的OEM厂商选择余地更大。即使有不同的电流要求,连接器也可以保持不变;只需要改变导线尺寸。单一重复使用连接器系统可以简化、加快设计和制造,同时也为OEM提供性价比更高的方案。能够支持和保持连接器指定的入口保护(IP)标准的导线尺寸范围特别有价值。
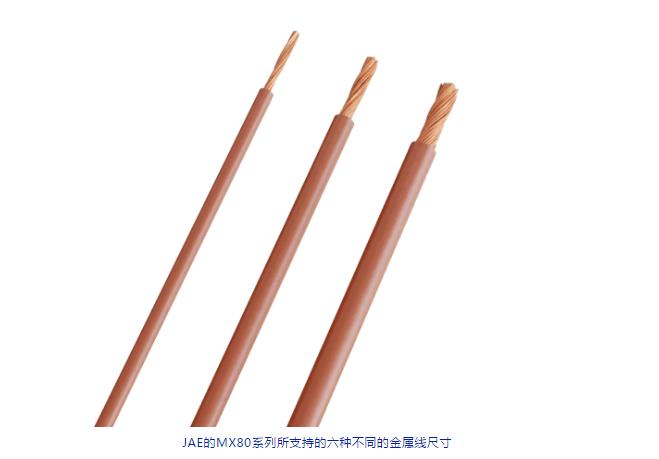
连接器系统的灵活性使得功能更强大和可集成性更高,以及更多的机会来改善电气设计和整体车辆体验。最终,连接器系统提供的灵活性越大,OEM制造商就越能节省空间、重量、时间和金钱。
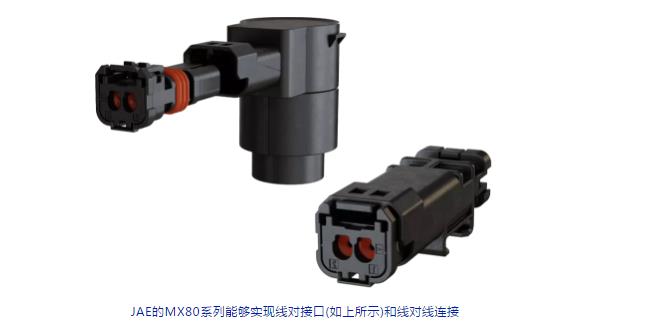
灵活性的例子包括诸如连接器位置保证(CPA)特性、极化和颜色编码选项,以及PCB插头和电缆继电器连接选项。连接器供应商增加更大的灵活性和多功能性。例如,扩大针数和增加更高温度的版本可以使设计人员能够随着技术的发展改进系统。
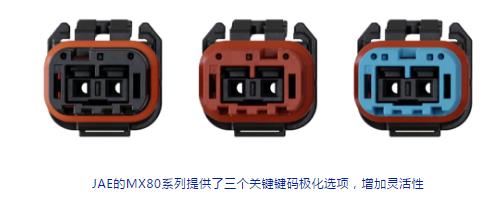
许多传统连接器正在被新系统和技术的新一代连接器所取代。研究所有可用的连接解决方案很有必要,能够为未来车辆的设计增加更多的选择。
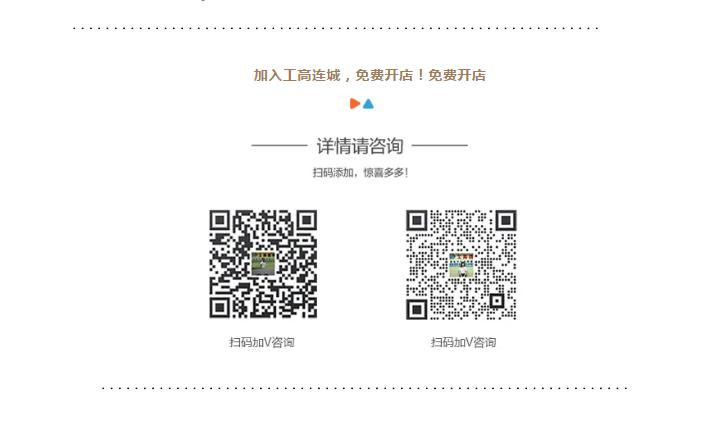